For electrode paste manufacturers, the two most dreaded issues are electrode soft break and hard break. Among them, soft break is more alarming as it can easily lead to accidents. Hard break occurs due to insufficient strength of the electrode paste after sintering. Soft break refers to the situation where the sintering speed of the electrode is slower than the consumption rate, causing the electrode to descend too quickly. Incomplete sintering prevents the electrode from withstanding tension and lateral impact from the lower part, resulting in fractures. These two problems directly affect the performance of the electrode paste and also influence operational practices during usage.
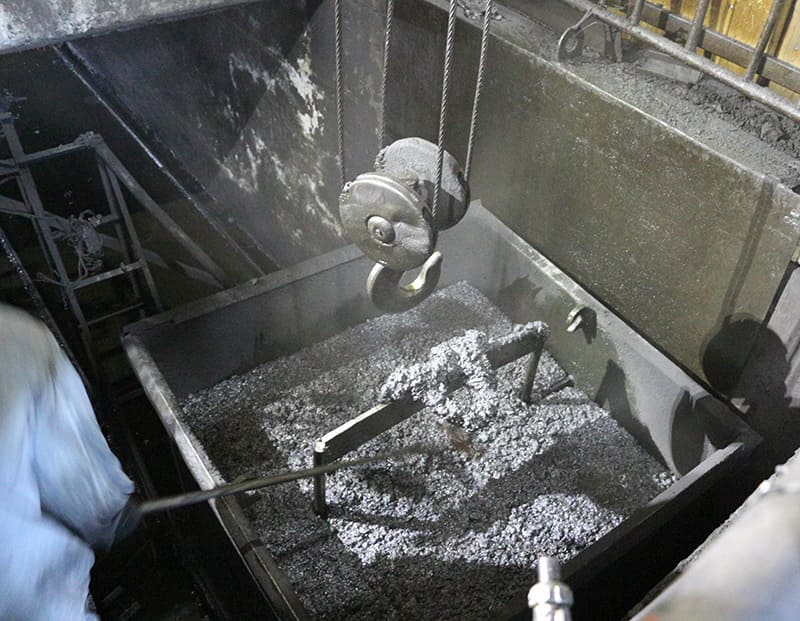
The production of electrode paste involves two main stages: batching and kneading. Currently, the kneading process is mostly standardized, as long as conventional equipment (intermittent dual-axis kneading pots with a capacity of 2000L or above) is used, and the kneading temperature and time are well controlled. The primary challenge in this stage is to address the components that contribute to the slow sintering speed of the electrode paste.
Some manufacturers adopt the method of reducing the amount of asphalt used. This approach is effective to some extent, but a reduced amount of asphalt leads to poor flowability of the electrode paste, making it difficult to fill the electrode cylinder, which can result in poor density after sintering and increase the risk of hard break.
Another method involves lowering the softening point of the asphalt and increasing the electrode sintering speed. However, the softening point of asphalt cannot be lowered indefinitely, as excessively low softening point asphalt will reduce the coking rate of asphalt, leading to a decrease in the strength of the electrode and still causing hard break.
Therefore, in the production of electrode paste, besides mastering the two methods mentioned above, it is essential to enhance the sintering speed of the electrode through formula adjustments. This can be achieved by incorporating highly conductive and thermally conductive graphite materials, which increase thermal conductivity and expedite the baking process. Simultaneously, minimizing electrode consumption is crucial to restrict the rate of electrode descent and achieve a balance between electrode consumption and sintering. For more detailed inquiries, feel free to contact Saxin Carbon, a manufacturer with over 20 years of experience in electrode paste production, to address various smelting issues.