Electrode paste plays a crucial role in the efficient functioning of electric arc furnaces, where it sinters within the electrode casing during operation. Understanding the heat sources responsible for baking the paste is essential for ensuring optimal performance and longevity of the electrodes. This article explores the three primary heat sources that contribute to the sintering process and their significance in the operation of furnaces.
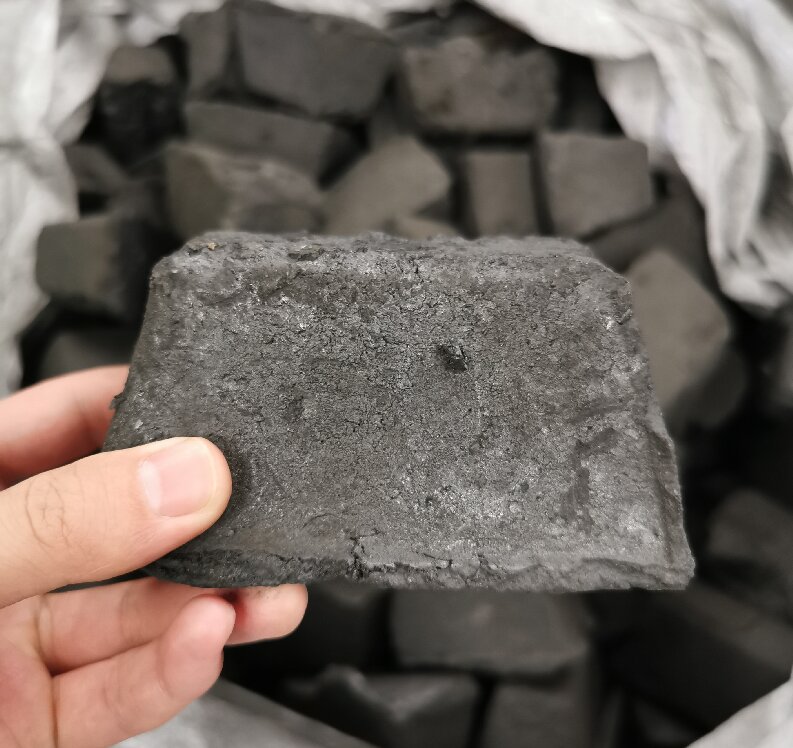
Electrode paste sinters within the electrode casing, and the heat sources come from three main aspects:
Heat conduction from the electrode body: At the electrode tip, an electric arc is generated, with temperatures reaching around 3500°C. Heat is conducted upwards from the electrode tip, so as the electrode paste moves downwards, the temperature gradually increases, leading to sintering. The conduction of arc heat is the primary source of the heat required for baking the electrode.
Resistive heat generated by the current passing through the electrode: As current flows through the electrode, a portion of the input power is converted into resistive heat due to the high resistance of the electrode paste itself, providing additional heat for baking the electrode.
Heat conduction and radiation from the furnace flames: The furnace surface temperature is very high, especially in open furnaces, where it typically ranges from 600 to 800°C. This heat is conducted and radiated to the electrode, particularly when the electrode is lowered, causing a rapid rise in surface temperature, which plays a significant role in the complete sintering of the electrode.
The baking of electrode paste relies on a combination of heat conduction, resistive heat, and the high temperatures radiating from the furnace flames. Each of these heat sources plays a vital role in ensuring the effective sintering of the paste within the electrode casing. By optimizing these factors, furnace operators can enhance electrode performance and ensure more efficient furnace operations.