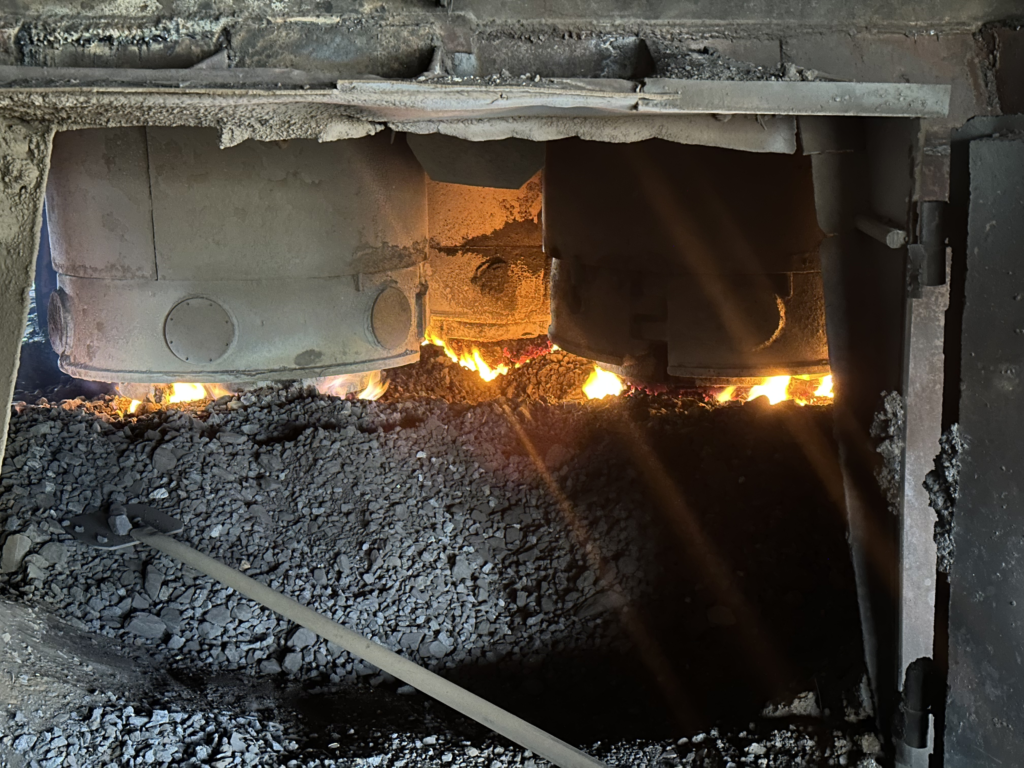
In the production process of calcium carbide furnaces, the baking of electrode paste is a crucial step. After being baked, the physical and chemical properties of electrode paste undergo significant changes, thus meeting the needs of efficient and stable operation of calcium carbide furnaces. Then, where does the heat source for baking electrode paste in calcium carbide furnaces originate? This article will delve into this topic.
First, one of the main heat sources for electrode paste baking is resistance heat. When current passes through the electrode paste, resistance heat is generated due to the electrode paste’s inherent resistance. This resistance heat is one of the primary heat sources in the electrode paste baking process, especially during the initial baking stage. The magnitude of resistance heat depends on the current flowing through the electrode paste, the resistance value of the electrode paste, and the duration of current passage. Therefore, in practical operations, the baking degree of electrode paste can be controlled by adjusting the current magnitude and baking time.
Second, conductive heat also plays a vital role in electrode paste baking. In calcium carbide furnaces, electrode paste is continuously used, and as the electrode wears down, fresh electrode paste is constantly added to the electrode. In this process, already baked electrode paste transfers heat to the newly added electrode paste through thermal conduction, accelerating its baking process. Additionally, the hot airflow inside the furnace also transfers heat to the electrode paste through conduction, further promoting its baking.
Moreover, radiant heat cannot be overlooked as a heat source for electrode paste baking. In the high-temperature environment of calcium carbide furnaces, furnace walls and other high-temperature components radiate heat into the surrounding space. While this radiant heat does not directly act on the electrode paste like resistance heat and conductive heat, it still exerts a certain influence on the baking process. Especially in the top region of the furnace, due to the radiation effect of the furnace walls and other high-temperature components, the temperature of the electrode paste is further elevated, accelerating its baking process.
In addition to the above three heat sources, other factors also influence the baking process of electrode paste. For instance, the composition of electrode paste’s raw materials, particle size distribution, additive types, and additive amounts all affect its baking performance. Moreover, operational parameters of the calcium carbide furnace, such as current, voltage, and furnace temperature, also influence the baking process of electrode paste.
In conclusion, the heat source for baking electrode paste in calcium carbide furnaces primarily originates from resistance heat, conductive heat, and radiant heat. Among them, resistance heat is one of the most significant heat sources, which can be controlled by adjusting the current magnitude and baking time. Conductive heat and radiant heat also affect the baking process of electrode paste to a certain extent. In practical operations, various factors need to be comprehensively considered to ensure that the electrode paste is sufficiently baked and meets the production needs of calcium carbide furnaces.