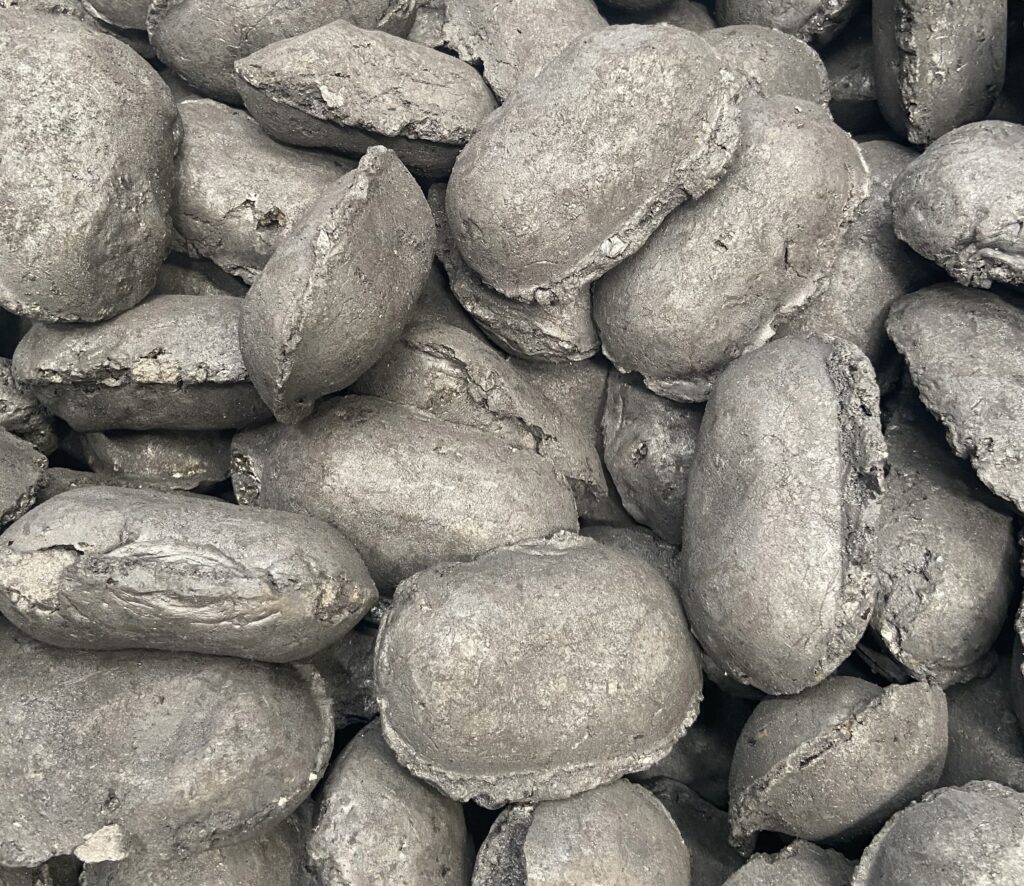
Electrode paste, as the essential raw material for self-baking electrodes, directly impacts the quality of electrode sintering and performance. Its quality is crucial not only for reducing paste consumption but also for ensuring the safe operation of calcium carbide furnaces. Electrode paste consumption reflects the overall technical management level of furnace operations and is a key indicator of production efficiency.
The main factors affecting electrode paste consumption in closed calcium carbide furnaces are as follows:
The quality of electrode paste significantly affects the sintering quality, consumption rate, and stable operation of the furnace. Ash content is a critical parameter as it impacts sintering speed, conductivity, oxidation resistance, density, and consumption. However, lower ash content is not always better. Extremely low ash content can weaken sintering strength, while excessive ash content may cause electrode breakage, increasing paste consumption. Properly controlling electrode paste quality is vital for long-term stable furnace operation.
Electrode accidents, such as soft or hard breaks, often result from insufficient attention to operational details, including inaccurate measurement of paste addition depth. Improper adjustments during the sintering phase can disrupt the thermal balance, making recovery challenging. High-current forced sintering leads to porous, weaker electrodes that consume faster. Frequent furnace stops due to accidents reduce production and increase paste consumption, making electrode accidents a major factor in excessive paste usage.
The paste column height refers to the distance from the top of the conductive element to the paste addition level, ideally maintained at 3.5–4.5 meters. The pressure on the paste per unit area should be 0.35–0.45 kg. Variations in paste granularity and bulk density affect consumption. Over-height paste columns increase the load on electrode holders and risk paste liquefaction, disrupting the sintering process and worsening electrode conditions. Conversely, under-height columns lead to rapid sintering, delamination, and reduced tensile strength, increasing the risk of breakage and higher paste consumption. Strict control of paste column height is essential for proper sintering and minimizing accidents, thus reducing paste consumption.
Want to know more? Please stay tuned for more factors in our next blog.